Proactive Maintenance to Shrink Truck Repair Costs
by
Yulia Miashkova
August 04, 2021
Truck maintenance is one of the least favorite parts of any fleet manager's job because it's so close to truck repair. It comes up when you least expect it, it disrupts the logistics operation, and it costs the business money that the business would rather not spend.
How do you minimize fleet downtime? How to account for wear and tear and make cost-effective managerial decisions? The answer is proactive maintenance. This here is a guide on how to implement your own preventive maintenance program.
What is fleet maintenance?
Fleet maintenance is, in its simplest form, everything you do to extend the life of a fleet of vehicles. No logistics operation can function without its fleet, and vehicle maintenance is crucial in keeping all logistics assets in top-notch condition.
Fleet maintenance comes in two types: proactive and reactive maintenance.
Proactive maintenance is also referred to as preventive maintenance as it relies on a maintenance schedule rather than performance failure. Reactive maintenance, on the other hand, is the type of maintenance management that is condition-based and occurs when a vehicle is not performing properly.
Most logistics organizations try to have a combination of both fleet maintenance types, having a custom maintenance strategy that consists of specific truck maintenance tasks.
Preventive maintenance might not be always realistic as fleet managers will usually focus on keeping their critical assets in top condition. However, it is miles ahead of reactive maintenance and it's more than doable with a good preventive maintenance schedule and the right safety management tools. Let's look into it.
Benefits of proactive maintenance
We'll now go over the obvious and not-so-obvious benefits of preventive maintenance that can be applied to trucks in particular and equipment in general.
Reduced repair costs
This one might seem a little too obvious but it's still worth talking about. Nobody likes truck repairs. Instead of holding on until you need to replace truck parts or entire vehicles, make sure you embrace proactive maintenance.
Checking on your trucks and their crucial parts like the engine at regular intervals is how you minimize the risk of things breaking and reduce the cost of repairs in the long term.
Extended truck life
Proactive maintenance is always a good idea when your goal is to extend the life and prevent the failure of your fleet. Running truck checks regularly means that you don't exhaust your system's resources by pushing it to the limits.
The same way you are recommended to do an oil change every 6 months instead of waiting for your engine to overheat, accounting for wear and tear in general and not waiting for things to break down is a safe bet.
Improved driver safety
Your equipment is never just an asset that may fail on you; it also determines the safety of the people who operate it. Reactive maintenance is never good for your driver staff as they've already been put in danger even if no accidents happened yet.
Sticking to a proactive maintenance program will keep your most important asset - your staff - safe and sound, and that's always good for your business and for your customers.
Increased service time
The less downtime your trucks sustain, the more time they're actually on the road carrying out orders. Commercial vehicle routing, especially when prescheduled, is a brilliant way to reduce cost per delivery. The amount of orders a truck can deliver is determined to a great extend by the state it's in. Having a robust proactive maintenance strategy will only serve you.
Lower operational costs
It might seem counter-intuitive but having more frequent truck checks will cost your logistics operation less than waiting for truck failures. Transportation management solutions like Track-POD that feature a delivery driver app are a brilliant way to incorporate proactive maintenance into every delivery route.
More on that later but let's just say that software like Track-POD lets you delegate proactive maintenance to the people driving the trucks, which means things will be performed quickly and as scheduled.
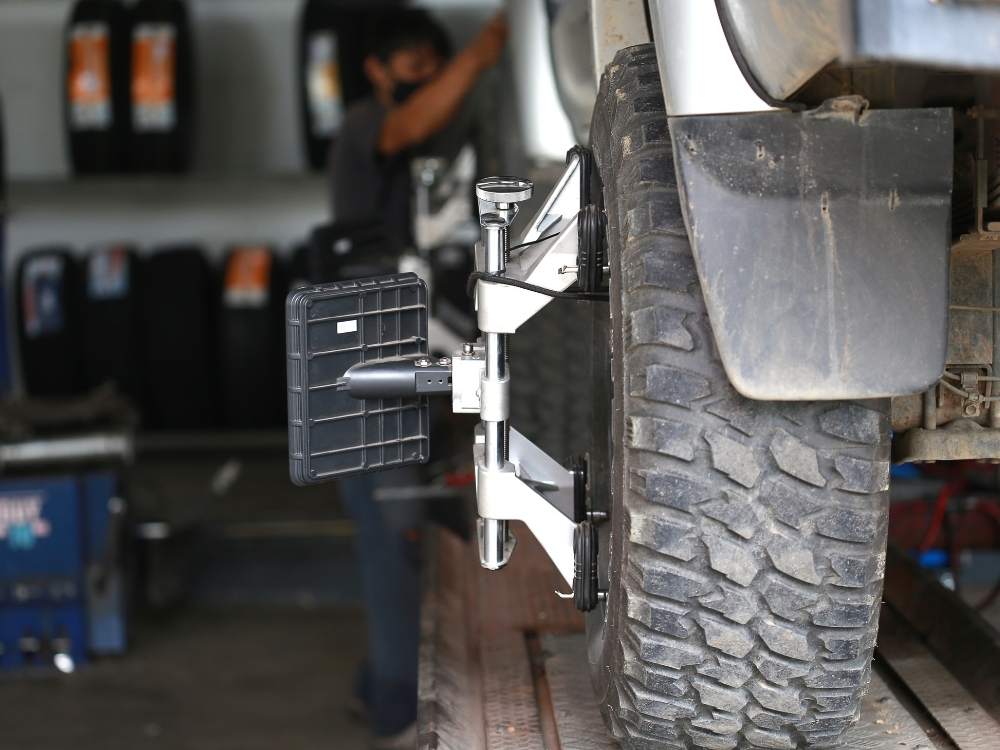
Truck maintenance checklist
Okay, we've established by now that proactive maintenance is a sure-fire way to keep your critical assets working for you and not against your budget. Let's review some of the basic steps and tips that go into a proactive maintenance routine for trucks.
Fluids
Fluids-related maintenance covers everything from under-the-truck leakage to engine oil, coolant, brake and transmission fluid, and windshield washer fluid. Keeping all your truck fluids clear is a great way to minimize wear and tear of your fleet assets and improve the quality of driving as well as overall performance.
Brakes
Performing brake maintenance requires some skill, so as a fleet manager, you might want to train your drivers on how to inspect brakes ahead of the summer and winter seasons. To run an essential brake check, your staff will need tools like rulers, chalk, and helpers. But once you've invested in training your drivers on brakes maintenance, you will receive dividends for seasons to come.
Tires
Tires are an essential yet vulnerable truck component that you always want to protect. From checking air pressure to making sure there are no objects inside tires that might harm the surface, proper tire maintenance keeps your trucks from failure and protects your assets.
Wiring
When we talk about electrical truck wiring, we usually focus on the battery, starter, and alternator. Proactive maintenance covers all of these things + other components of the electrical system such as the windshield wipers, headlights, and even the brake controller.
Emission control
Not all logistics operations can move to the carbon-neutral shipping model overnight. Still, we are encouraged and even enforced to implement some form of emission control. Be it diesel particulate filter, diesel exhaust fluids, or selective catalytic reduction systems you have on your fleet, you need to keep an eye on those and incorporate their maintenance in your overall proactive maintenance strategy.
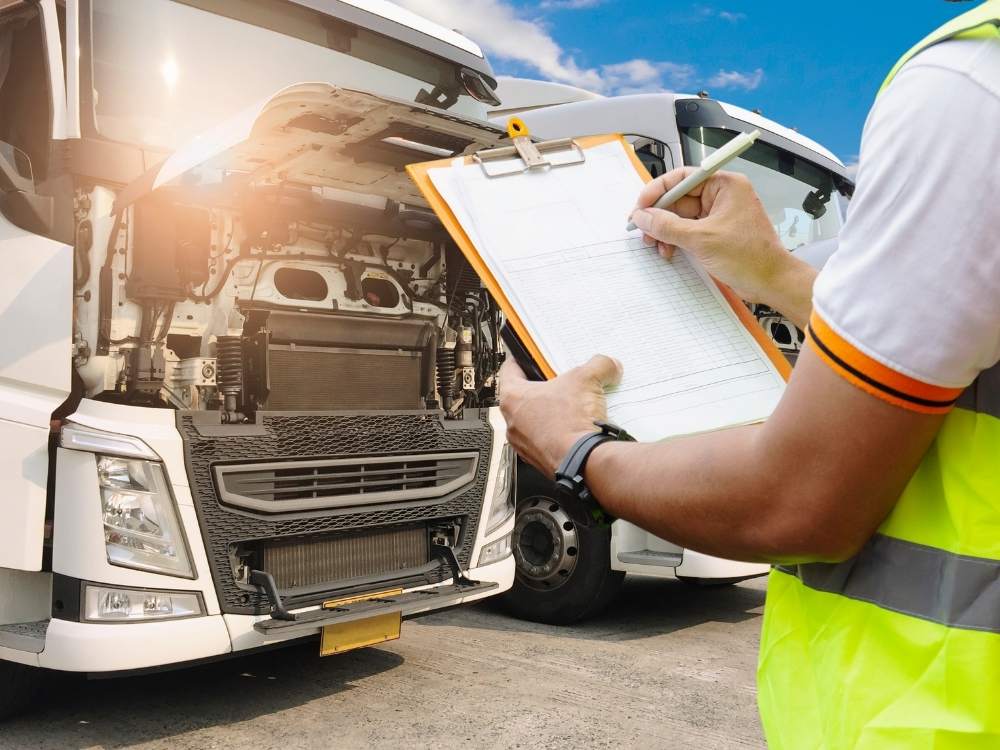
3 steps to avoid commercial truck repair
Now that we've covered all major bases of proactive maintenance for commercial trucks, it's time to put things into action. Let's see how you can use transportation management software like Track-POD to schedule and implement a proactive maintenance program for your fleet. Sticking to a proactive maintenance strategy will protect your equipment and assets and reduce the instances of truck repair.
1.Specify vehicle check criteria
When you're using the Track-POD dispatcher web dashboard, you can make vehicle maintenance an essential part of every delivery route. This makes fleet management a lot easier as you delegate truck maintenance to your courier drivers. To get started, head over to your Settings menu and locate Vehicle Check, which is where you specify your maintenance criteria.
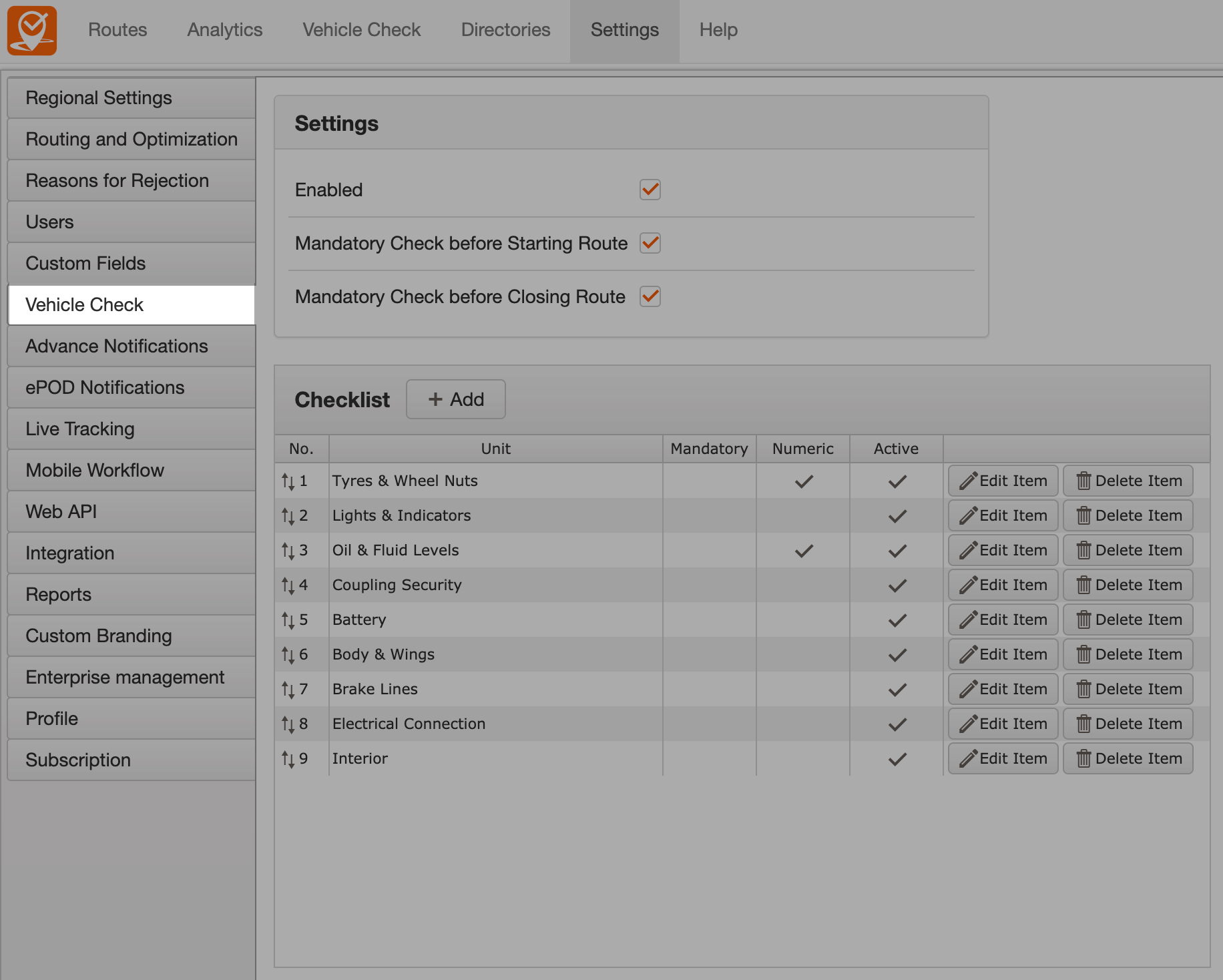
There, you can see three checkboxes that stipulate that maintenance becomes mandatory and needs to be completed by drivers before and after each delivery route. Below, you have a proactive maintenance checklist that you can adjust according to your resources.
Specify your proactive maintenance criteria and make sure you include all essential things like oil level, tires, battery, brake lines, coolant, etc. The best thing is that you can extend the maintenance list as much as you want, adding new maintenance criteria and specifying the Warning and Critical values along the way.
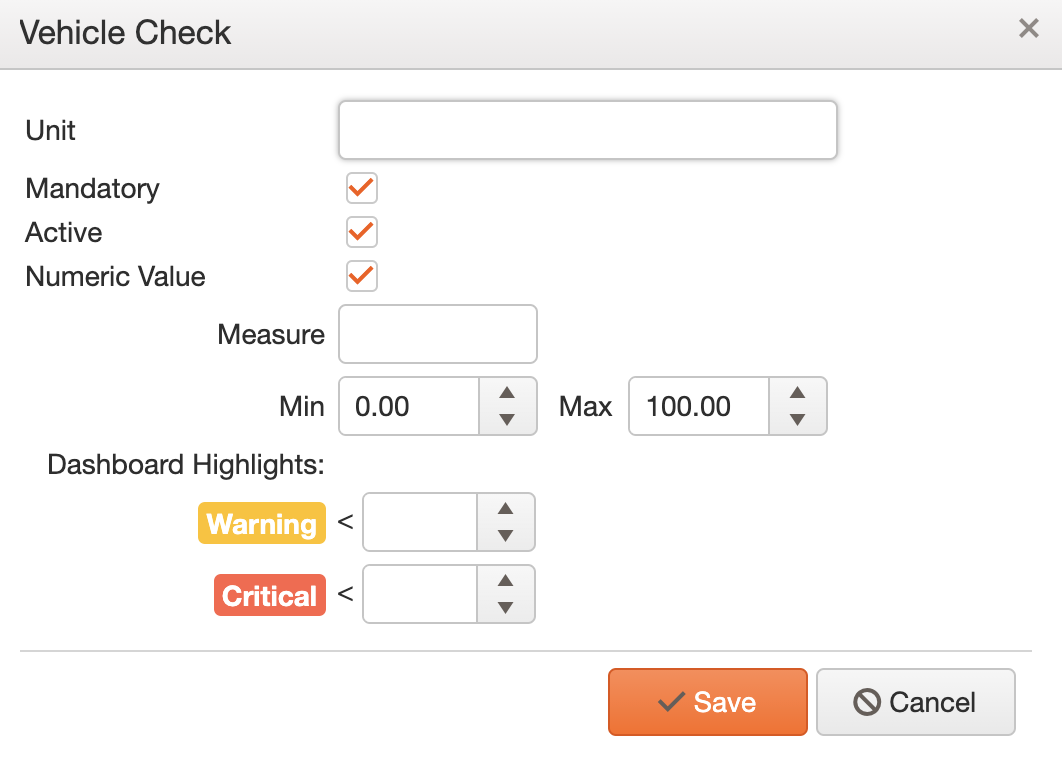
Track-POD makes it easy to introduce proactive maintenance into your truck drivers' routine because all the criteria you set in the web dispatcher dashboard will be automatically reflected in Track-POD's driver app.
2.Add proactive maintenance to daily routes
Once your drivers have their proactive maintenance checklists in their driver app, they're obligated to run truck checks before and/or after each delivery route. This is what it looks like on the driver's side.
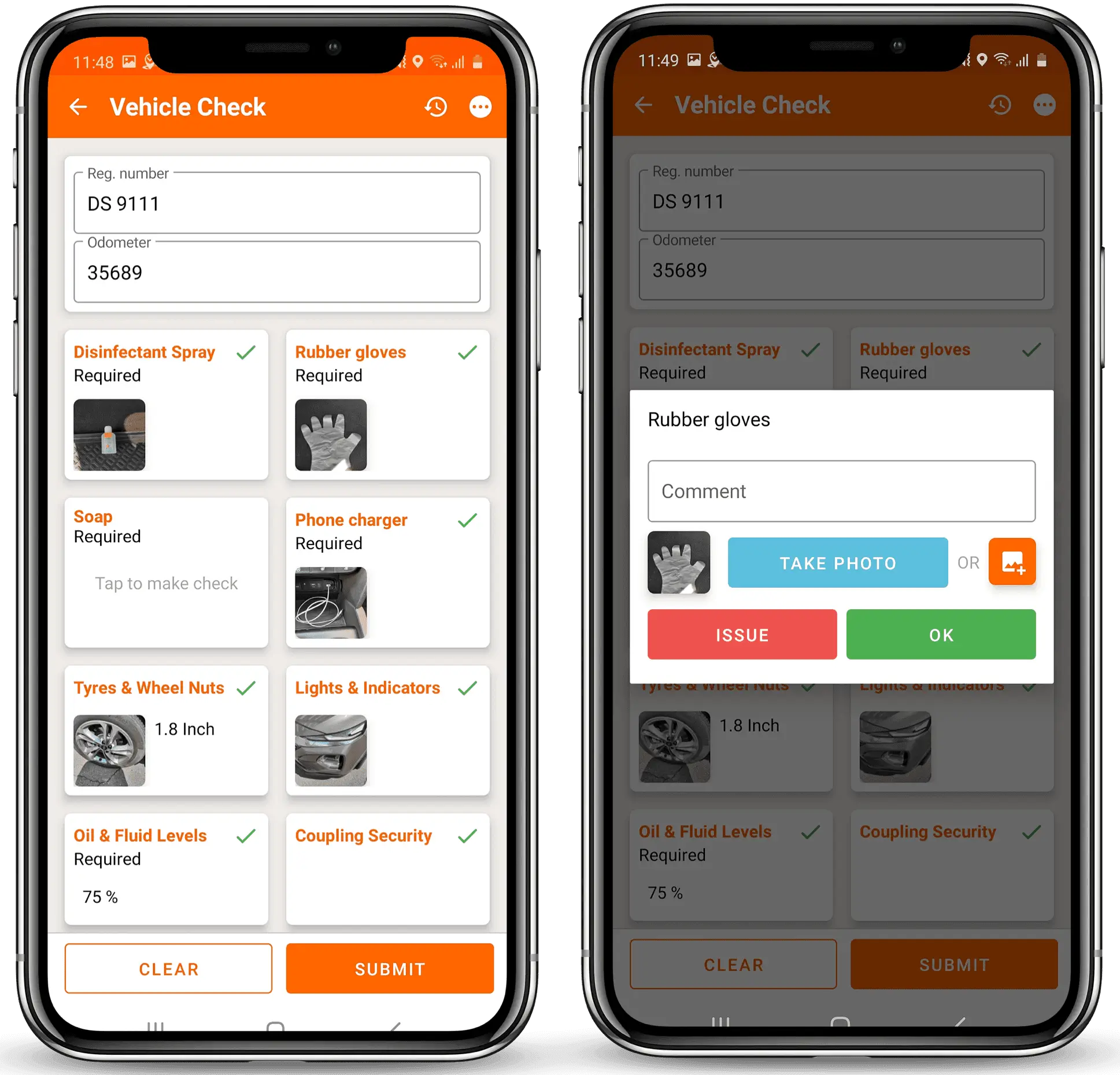
As you can see, the driver needs to run proactive maintenance following the checklist that you created for them. If you choose to make truck maintenance obligatory before and after each route, you'll have your couriers regularly check on the equipment that they're operating, which will greatly reduce the overall downtime.
3.Use analytics to keep an eye on critical values
Making truck maintenance a part of daily delivery routes makes your job a lot easier. Track-POD shipment analytics and maintenance analytics are both parts of the web dispatcher dashboard that stores all data on individual driver performance, failure rate, system issues, shipment documentation, and truck maintenance.
Because you've specified Warning and Critical values for truck maintenance criteria, you'll have this data reflected in the web dashboard, which means you can instantly see which truck needs reactive maintenance. Using the filter option, you can also reorganize maintenance data by columns and attend to the critical assets first.
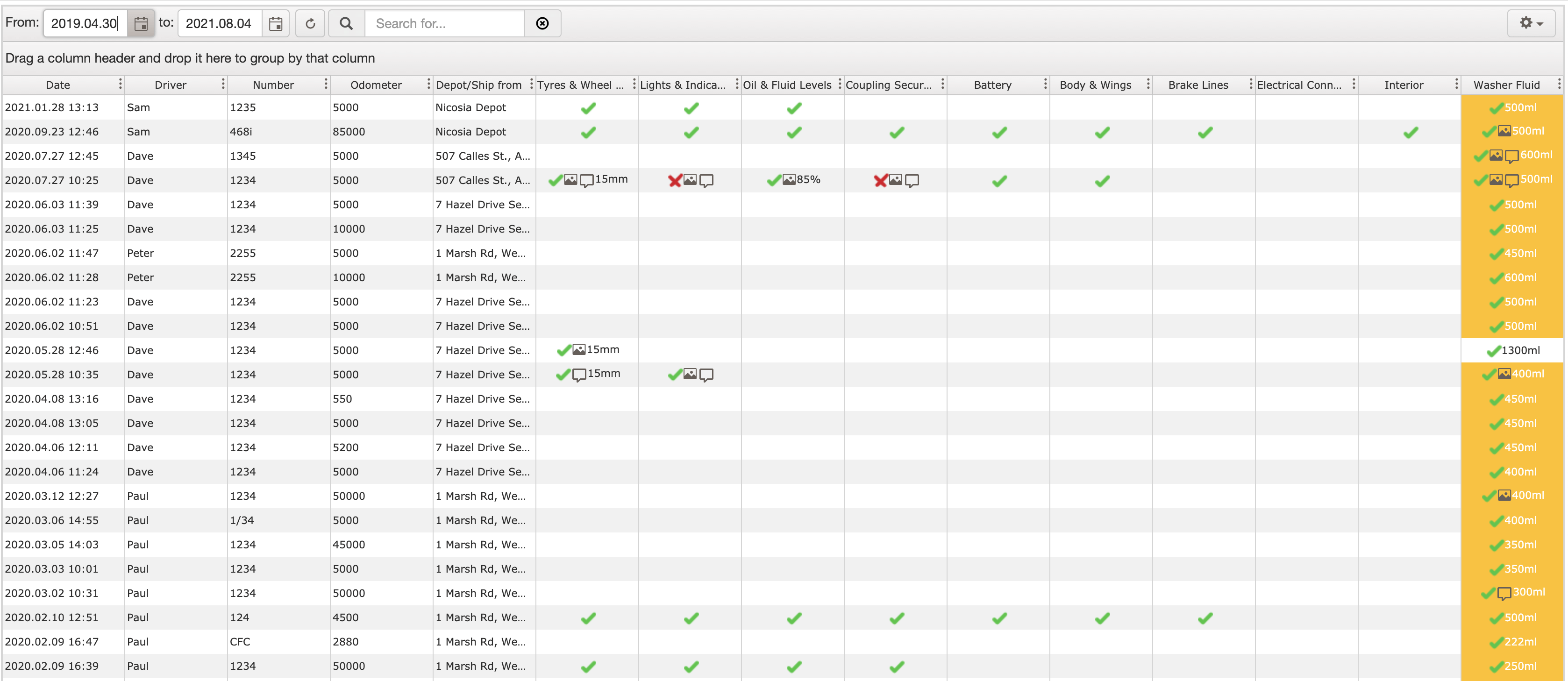
Having all maintenance data in one dashboard means you have the full overview of your fleet and can foresee any downtime weeks and months ahead. This keeps your whole logistics system from failures and ensures the top quality of your service with minimum operational costs.
Recap
Proactive fleet maintenance is how you take the best care of your equipment and tools through scheduled checks that are performed by your driver staff and designated mechanics in case of failure. A scheduled maintenance program doesn't have to take tons of time and resources. In fact, you can implement one at no additional costs yet with all the benefits of an efficient maintenance routine.
- First, you specify the maintenance criteria in your Track-POD web dispatcher dashboard.
- Then, you have your drivers follow the maintenance checklist and run truck checks before and/or after each delivery route.
- Last but not least, you keep an eye on all maintenance data in your web dashboard, which means you're always aware of assets that need urgent attention outside of your maintenance schedule.
I hope this guide inspires you to make proactive truck maintenance a part of your drivers' daily routine. If you need help setting up a truck maintenance checklist or accessing maintenance data in your web dashboard, get in touch with our team and let's make proactive maintenance work for you.
P.S. If you're looking for pointers in choosing fleet maintenance software, check out this graphic provided by Crazy Egg.
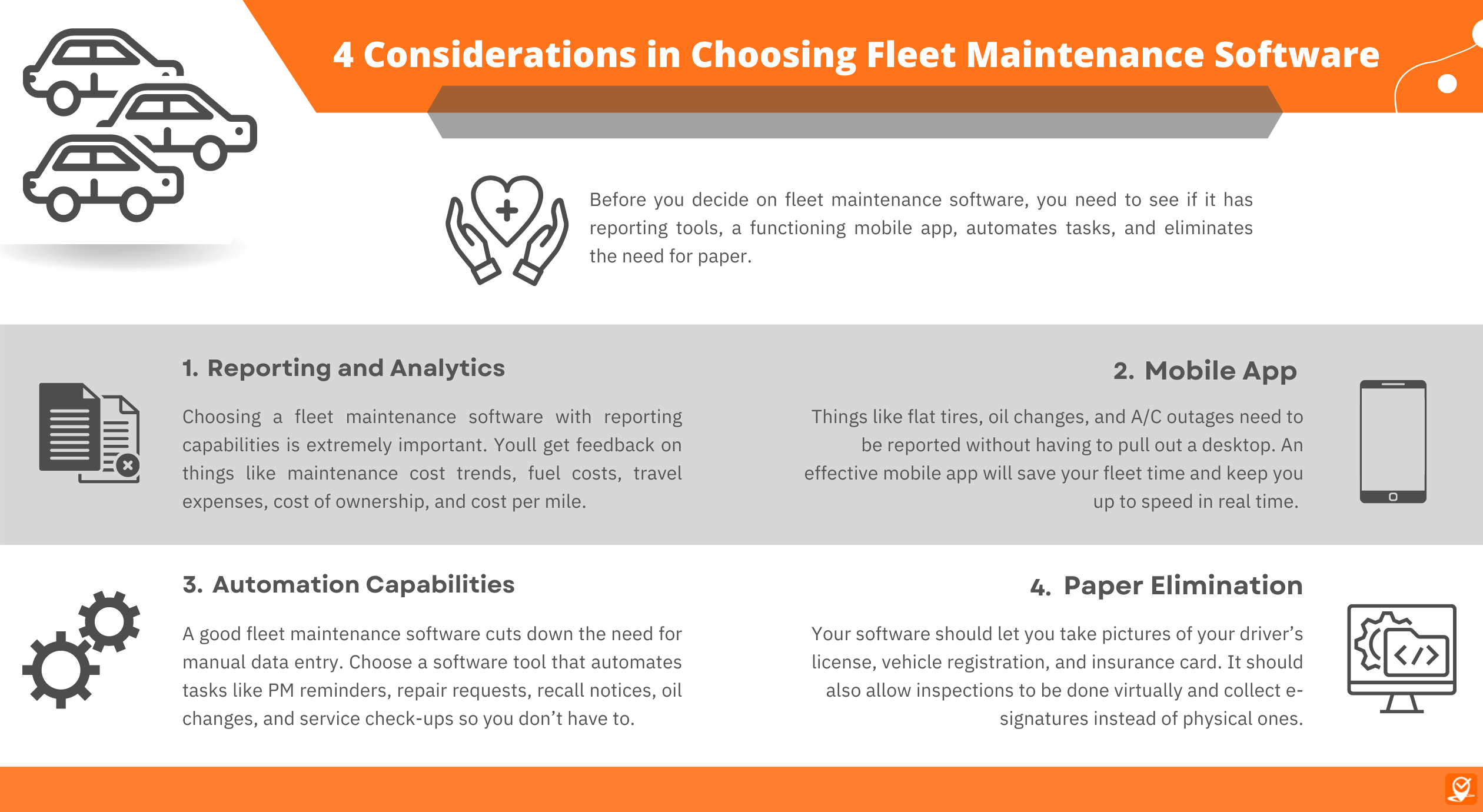
- Transportation management
About The Author
Yulia Miashkova
Growth marketing manager with a background in public relations, SEO, social listening, and Account-Based Marketing.